5 Things You Need to Know from the Digital Twin Readiness Guide
Decoding Digital Twins for Your Organization
One of the most transformative technologies in the water industry today centers around planning and implementing Digital Twins. Benefits of this technology include increased speed of delivery, improved compliance, better allocation of resources, and greater return on investments in workforce and infrastructure assets.With so many competing priorities in day-to-day operations, how can your organization get ahead of the curve in implementing a Digital Twin? The industry’s first Digital Twin Readiness Guide can help you to get started and make the most of your investment.
Digital Twin technology can revolutionize the way systems are managed, and now there is a standard guide to reference when beginning your Digital Twin journey – the SWAN Digital Twin Readiness Guide (pictured at left).
In partnership with the Smart Water Networks Forum (SWAN) Digital Twin Group, Brown and Caldwell (BC) led the development of the official Digital Twin Readiness Guide. This Readiness Guide is an industry resource developed over the past 18 months with contributions from 49 companies through 70 meetings and 14 workshops. This Digital Twin Readiness Guide provides a much-needed consolidated resource for utilities to reference as they upgrade and expand their operational systems.
The Digital Twin Work Group, in partnership with the SWAN Digital Twin Utility Advisory Group and American Water Works Association Digital Twins Committee, has established an official definition of a Digital Twin as: a dynamic digital representation of real-world entities and their behaviors using models with static and dynamic data that enable insights and interactions to drive actionable and improved outcomes.
The Digital Twin Readiness Guide supports the implementation process with tangible case studies and impactful resources to help you get the most out of your system. Let’s break down the top five things you need to know to get started on your journey.
1. Accelerate Beyond the Conventional
Improve operational efficiency beyond conventional models with Digital Twins.
Digital Twins are built from a composite of many separate applications and data sets. This involves technology providers, engineering companies, water system staff, and others. This infographic from the Readiness Guide shows key distinctions between a conventional model and a Digital Twin:
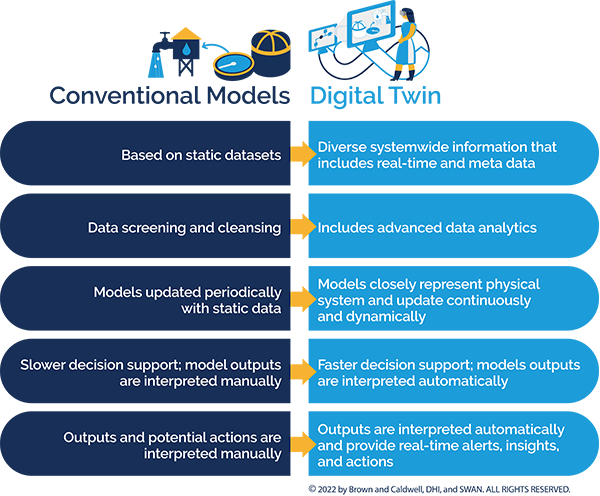
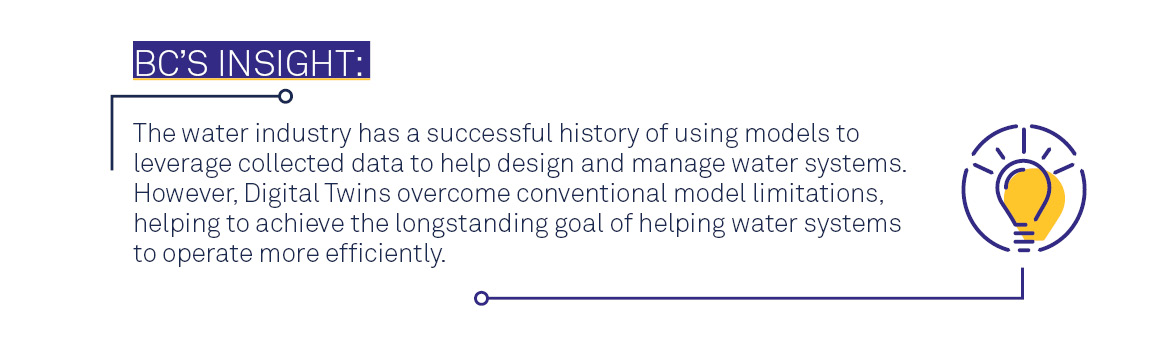
2. Your Team is More Ready Than You Think
Empower your team with technology they are already leveraging with Digital Twins.
While there are many nuances to a Digital Twin, many of the foundational concepts of how Digital Twins are used and applied already exists in how your current team acts in their daily lives. Your team may have even used a Digital Twin before they arrived at work today. If they leveraged a map application on their cell phone to understand the traffic congestion on their route or identified where along their route to stop for fuel, they were using a Digital Twin. Their devices were capturing information about their location, speed, and direction they were heading, representing the physical world around them to better prepare them for their journey to begin their work. Similar to a smartphone’s map application, a Digital Twin of your organization could leverage existing GIS data you may already have and the current staff location in the field with other critical information, such as customer complaints, water quality samples, or maintenance work orders. A Digital Twin at your organization can create a similar experience for your staff and your systems.
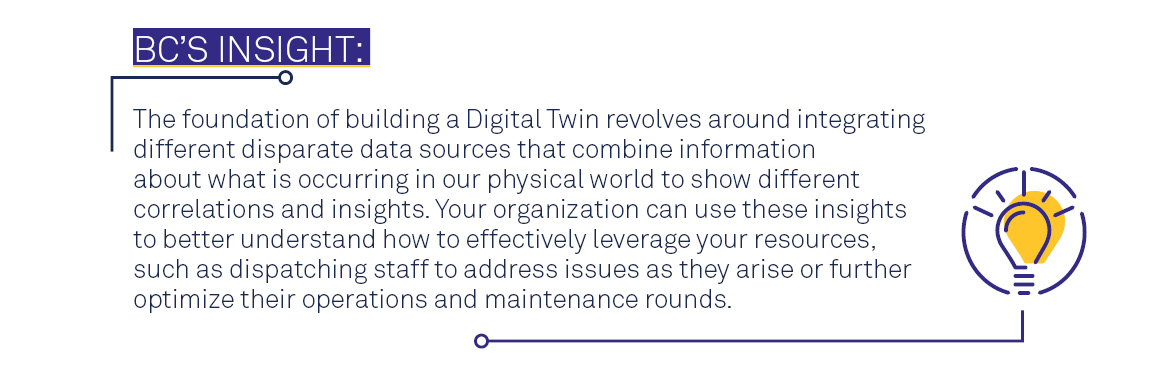
3. Start With the Tools You Have
Leverage your current asset management and technology resources to start your Digital Twin journey.
Every water system has various technologies in place for asset management, operations support, and maintenance needs. Transitioning to a Digital Twin doesn’t mean these investments need to be abandoned, on the contrary, this existing data infrastructure can feed into a Digital Twin so you can get the most of your previous investments.
These systems that water organizations typically already have include customer management systems, SCADA systems, GIS, and computerized maintenance management systems. Your organization may also have a biological or hydraulic model. These systems each have immensely valuable information used by different parts of your organization and can be leveraged together to serve as the basis for your Digital Twin.
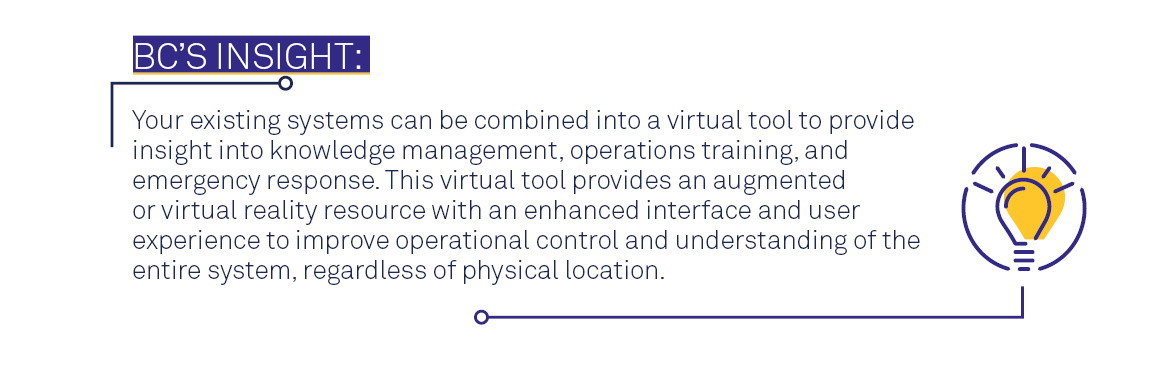
4. Set Clear Goals and Define Your Outcomes
Know where you are going and use the power of Digital Twins to get you there.
A Digital Twin isn’t something you can simply “buy,” but is instead a journey towards each organization’s desired outcomes. Many organizations may not even know what outcomes are possible. The key to a successful implementation begins with a prioritized list of your desired outcomes that are the best fit for your current and future facilities, existing software, infrastructure, budget, and any other specialized factors.
While the path to implementing a Digital Twin is unique to each organization, the steps toward successful adoption are foundationally the same. Each implementation journey is scalable and iterative, following the same core path:

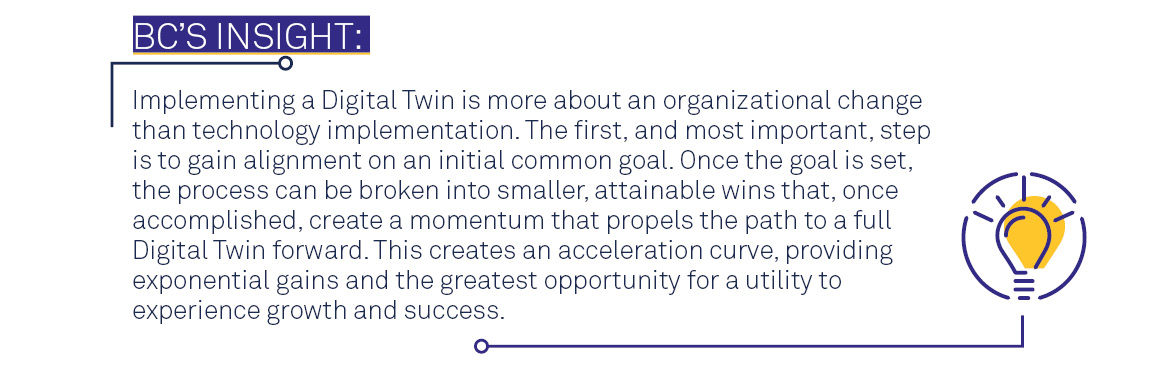
5. You Don't Have to Be an Expert
Let the experiences of others implementing Digital Twins be your guide.
Leveraging the lessons learned by other facilities is a great way to get a head start on your Digital Twin. The Digital Twin Readiness Guide provides 10 case studies covering a variety of organizations, needs, processes, and outcomes. Reference the Digital Twin Readiness Guide for summaries of these 10 case studies that include wastewater treatment, urban drainage, water network/water treatment, and pump station optimization projects.
A shining example of Digital Twin technology is the Water Corporation of West Australia project, as part of BC led Water Research Foundation 4917, that implemented Digital Twin using Innovyze’s IW Live ProTM and Info360TM Platforms for real-time distribution system model focused Digital Twin.
The project implemented a real-time hydraulic model using InfoWorks Live ProTM technology to reduce pipe breaks and water loss by monitoring system performance, e.g., water usage, leaks and pipe bursts, and infrastructure leakage index. The solution for burst detection identified a simulated burst in distribution pipe mains, demonstrating the value of the technology for large leaks and pipe breaks.
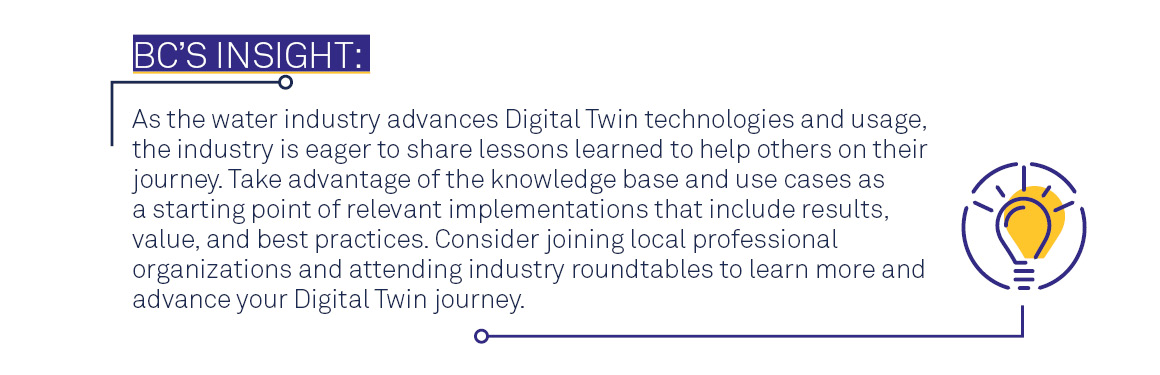
Conclusion
Water systems of all sizes face unprecedented challenges from increased costs, greater customer expectations, aging assets, and knowledge retention. Digital Twins offer a promise to revolutionize the way water systems are managed and provide a path to best leverage this technology so operational staff are fully supported.
The primary question is not if water organizations can benefit from a Digital Twin, the question is when is the best time to start the implementation? And for most organizations, the right time to take the first step is now.
Start the Conversation
Reach out to one of BC’s experts to get the conversation started about your organization’s Digital Twin journey. While the path to implementing a Digital Twin is unique to each organization, the steps toward successful implementation are foundationally the same. BC’s approach to Digital Twins centers around establishing the right foundation by conducting pilots and planning engagements to help organizations understand and adopt Digital Twins paired with a clear plan, goals, and outcomes. Our Digital Twin experts can talk through options to help advance your Digital Twin journey that make sense for your organization based on your unique desired outcomes.
Michael Karl is based in Portland, Oregon and is BC’s National Optimization Services Leader (BC:Opta) and a senior project manager who leverages digital technology in a sustainable way to better serve the unique challenges of the water industry. He has been providing automation and digital services to the water industry for the last 22 years.
Pusker Regmi is based in Columbia, Maryland. He specializes in wastewater process intensification and is a licensed environmental engineer in three states, a board-certified environmental engineer, and holds a doctor’s and master’s in environmental engineering as well as a bachelor’s in electrical engineering.
Alan Tucker is based in St. Louis, Missouri, Alan is BC’s Technology Planning Solution Lead and a business consultant who specializes in technology strategy and innovation. Alan spent nearly twenty years in the IT department of the Metropolitan St. Louis Sewer District, has a thirty-year career in environmental IT, holds degrees in English and political science, and has a unique, holistic approach to utility performance and digital water.